Лазерный станок по металлу (для резки стали, алюминия, меди и т.п.)
Лазерный станок по металлу (для резки стали, алюминия, меди и т.п.)
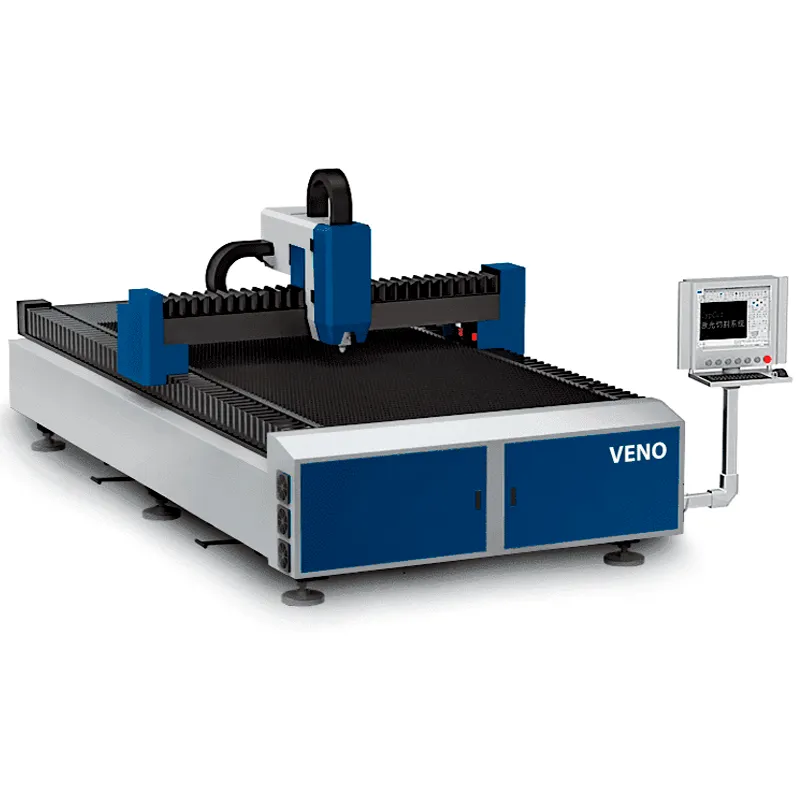
В наличии более 30 лазерных станков по металлу, опытный сервис! Цена от 1 789 050р! Бесплатные ПНР, возможно обучение, ввод оборудования в работу. Лазерные станки для резки металла необходимы для изготовления электрошкафов, кабин, корпусов, когда нужно выполнять резку листа, перфорацию и другие операции с металлоконструкциями.
Подбор по параметрам
Лазерный станок по металлу — это ключевое оборудование в любой современной металлообрабатывающей отрасли. Изготовление изделий из металла начинается с раскроя листового материала, и только лазерный станок по металлу обеспечивает высокую точность и качество резки без дополнительной обработки. Наши лазерные станки по металлу прошли строгий контроль качества как на заводах-производителях, так и нашими специалистами после поставки. Мы не просто продаем оборудование, мы сами используем его в работе, проводим ПНР и обучение персонала, что позволяет предлагать только проверенные модели по выгодным ценам.
Наши станки широко применяются в:- Машиностроении
- Медицинской промышленности
- Рекламном производстве
- Производстве торгового оборудования
- Изготовлении корпусов различного назначения
- Создании вентиляционных систем
- Строительстве металлоконструкций
- Производстве трубопроводов (отводы, тройники, опоры)
- Электронике и бытовой технике
Почему стоит купить лазерный станок по металлу?
Если вы задаетесь вопросом, какой лазерный станок по металлу купить, обратите внимание на преимущества этой технологии:
- Высокая надежность и долговечность. Лазерный источник работает более 100 000 часов без потери мощности.
- Минимальная себестоимость реза. Низкое энергопотребление и высокая скорость работы.
- Простота эксплуатации. Оборудование легко освоить даже новичкам. Редкие сервисные интервалы.
- Точность и стабильность. Высокое качество резки сохраняется на протяжении всего срока службы.
- Компактность. Экономия площади цеха за счет небольших габаритов.
- Энергоэффективность. КПД до 53% — один из самых высоких показателей среди аналогов.
Как выбрать лазерный станок по металлу правильно?
Чтобы выбрать лазерный станок по металлу и не переплатить, важно четко понимать свои задачи: объем производства, требования к точности и типы материалов. В зависимости от этого подбираются основные компоненты станка:
- Станина. Основа конструкции, влияющая на жесткость и точность. От нее зависит стабильность параметров резки.
- Лазерный источник. Производители: IPG, Raycus, MaxPhotonics. Мощность от 500 Вт до 120 кВт. IPG отличаются стабильностью и подходят для цветных металлов.
- Режущая голова. Может быть с ручной или автоматической фокусировкой. Используются модели: RayTools, SWX, Precitec.
- Система управления. CypCut, CypOne и NcEditor (Bodor Pro 2) обеспечивают простоту работы и автоматизацию процессов.
- Периферийное оборудование. Чиллеры, поворотные столы, защитные кабины и другие устройства, которые значительно ускоряют работу.
Какой лазерный источник лучше для станка по металлу?
IPG, Raycus и MaxPhotonics — лидеры рынка. Источники IPG имеют минимальную деградацию мощности (3,5% в год), а также устойчивы к отражению луча, что особенно важно при работе с медью и алюминием. Raycus и MaxPhotonics — более бюджетные варианты, но требуют большей мощности для обработки отражающих материалов.
Какая система управления подходит вашему станку?
CypCut — профессиональная система управления с функциями Nesting, автообрезки и оптимизации чертежей. Для базовых задач подойдет бюджетная версия CypOne. Полный функционал доступен в CypNest, который позволяет заранее задавать параметры резки и минимизировать простой.
Нужен ли сменный стол для лазерного станка?
Автоматическая смена столов (паллет) позволяет сократить время простоя на 15–20%. Это особенно актуально при высокой загрузке оборудования.
Как подобрать двигатели для лазерного станка по металлу?
От скорости перемещения головки зависят общая производительность и эффективность. Сервоприводы предпочтительны для крупного производства, шаговые моторы — для средней нагрузки. Более мощные двигатели обеспечивают высокую точность и ускорение.
Зачем нужен стабилизатор напряжения?
Любые скачки напряжения могут повредить дорогостоящее оборудование. Рекомендуется использовать стабилизатор с запасом мощности (на 20% больше суммарной потребляемой энергии). Например, для станка мощностью 8 кВт потребуется стабилизатор на 9,6 кВт.
Как рассчитать скорость резки на лазерном станке?
Учитывайте не только текущую мощность излучателя, но и прогнозируемую деградацию. Запас мощности гарантирует долгий срок службы и высокую скорость на начальном этапе.
Как оптимизировать загрузку и выгрузку материалов?
Для больших листов используют кран-балку, консольные краны, вакуумные траверсы или магниты. Хранение можно организовать с помощью автоматизированных стеллажей и транспортеров.
Какие вспомогательные газы используются в лазерных станках?
Для резки применяются кислород, воздух и азот. Газ хранится в баллонах, моноблоках или криоцилиндрах. Предпочтение отдается вариантам с клапаном и датчиком давления.
Какие металлы можно резать на волоконном лазере?
- Черные металлы: нержавеющая, углеродистая, инструментальная сталь.
- Ферросплавы: чугун, титан.
- Цветные металлы: медь, алюминий, цинк.
Зачем нужны ламели для лазерного станка по металлу?
Ламели из алюминия с треугольным профилем обеспечивают минимальный контакт с заготовкой и снижают риск отражения луча. Они легкие, удобные в обслуживании и повышают качество готовых деталей. Анодированные ламели еще более устойчивы к износу.
Если вы хотите купить лазерный станок по металлу с максимальной эффективностью, обратитесь к нашим специалистам. Мы поможем подобрать оборудование под ваши задачи, организуем доставку, установку и обучение работе с ним. Сделайте первый шаг к точному и высокопроизводительному производству уже сегодня!